What can help US manufacturing shortages?
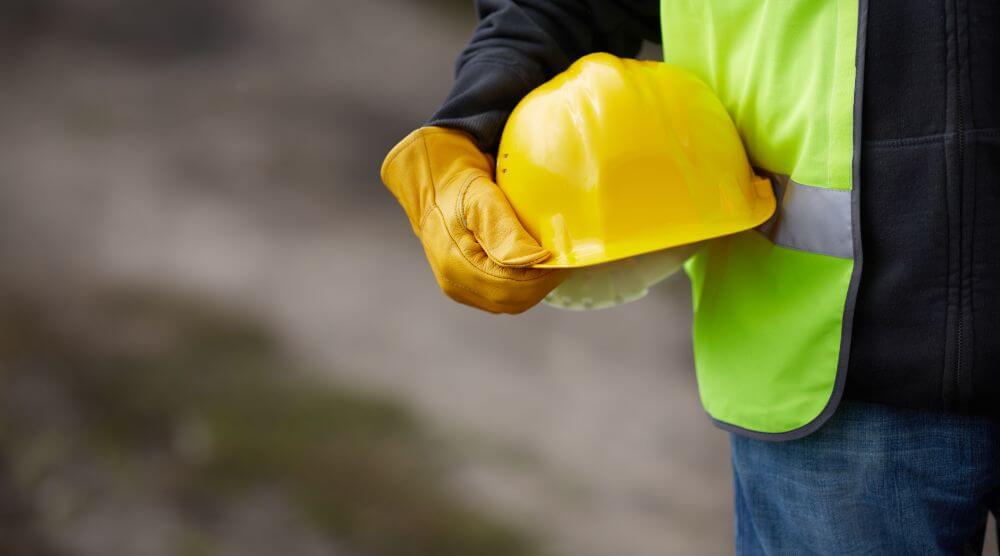
Published:
A year ago, few people outside the shipping or manufacturing industries had heard the term supply chain, let alone manufacturing shortages.
Massive supply chain shortages emerged in the wake of pandemic lockdowns that shut businesses worldwide and kept workers at home.
There were hopes that supply chain issues would start to abate in the first half of 2022 as the effects of the pandemic became contained in more countries. But other events, such as the war in Ukraine, have added new bottlenecks. And with lockdowns in Shanghai and other key cities across China, pandemic-driven snags are hurting supply chains again.
Shortages have come thick and fast across the board, from the looming Sriracha shortage that has hot sauce lovers feeling fiery to more pressing manufacturing shortages—both leaving companies with delayed deliveries, overworked staff, and an intensified level of uncertainty.
As much as we would love this blog to be about Southern California-based Huy Fong Inc and its beloved products, we will be taking a deeper look at how these shortages have affected manufacturing in the US. We will look at what the National Institute of Standards & Technology (NIST) has put in place to stimulate production.
Who has felt the brunt of manufacturing shortages most?
Semiconductors have been one of the most significant sources of global supply chain snarls, affecting a wide spectrum of industries. These include mobile phones, autos, and even lightbulbs.
Computer and tech companies have been struggling to keep up with roaring demand that started when workers shifted to working from home. Coronavirus factory shutdowns slammed chipmakers, also known as foundries, capacity to produce, leading to a backlog of orders.
In the U.S., Ford and General Motors are still stumbling because of parts shortages in recent months.
In late March, a lack of semiconductors forced Ford to halt production at its Flat Rock, Michigan, plant, where it manufactures Mustang vehicles. Likewise, General Motors shut down production at its Lansing Grand River assembly facility due to a “temporary parts shortage,” Reuters reported.
But, what could all these shortages mean?
According to Christian Lanng, CEO of platform for supply chain payments Tradeshift, an overhaul of the whole landscape is required.
“I honestly think we need to put manufacturing far from home to bed for good as it has had a horrible impact on the world,” he says. “Shipping goods all over the world came with a massive carbon footprint, not to mention the damage it has done to labour costs being pushed to [very low levels].
“Resilience needs to be a consideration across the board, economically, sustainably, ecologically and politically. The good news is that we have the technology to make this shift happen now, to build more regional manufacturing hubs that use rails rather than trucks, for instance. It is paramount to decentralize.”
Lanng explains how old governments built the old supply chain model around a post-war world that was stable and predictable. That world no longer exists, and adaptability is now more critical than ever.
What is alleviating this supply chain madness?
The issue could be the structure of the supply chain, as Christian explained, and the government has responded.
Working on decentralization, The US Department of Commerce’s National Institute of Standards and Technology (NIST) has awarded a total of $2.08 million to seven organizations in six states to develop manufacturing technology roadmaps to strengthen US innovation and productivity across entire industry sectors.
This is the second round of grants awarded to universities, industry and nonprofit organizations through NIST’s Advanced Manufacturing Technology Roadmap Program (MfgTech).
Each award of up to $300,000 will fund projects for up to 18 months to address national priorities such as manufacturing of critical infrastructure, communication, and transformative approaches and technologies in construction.
Furthermore, incentives for domestic semiconductor firms to expand production in the US may also be on the way from the government. A bipartisan bill to provide roughly $52 billion in investment to improve semiconductor production in the US is undergoing review.
On the talent side, workforce development is essential to secure the future of healthy and reliable supply chains.
The industry needs to make an effort to make warehousing and logistics jobs more attractive and turn them into a career choice rather than just a job. A supply chain worker learns many transferable skills to other professions, such as understanding inventory and gaining optimization techniques.
If you would like to join us for a live and exclusive webinar with manufacturing kingpins, Weinig Holz-her, you can sign up below: